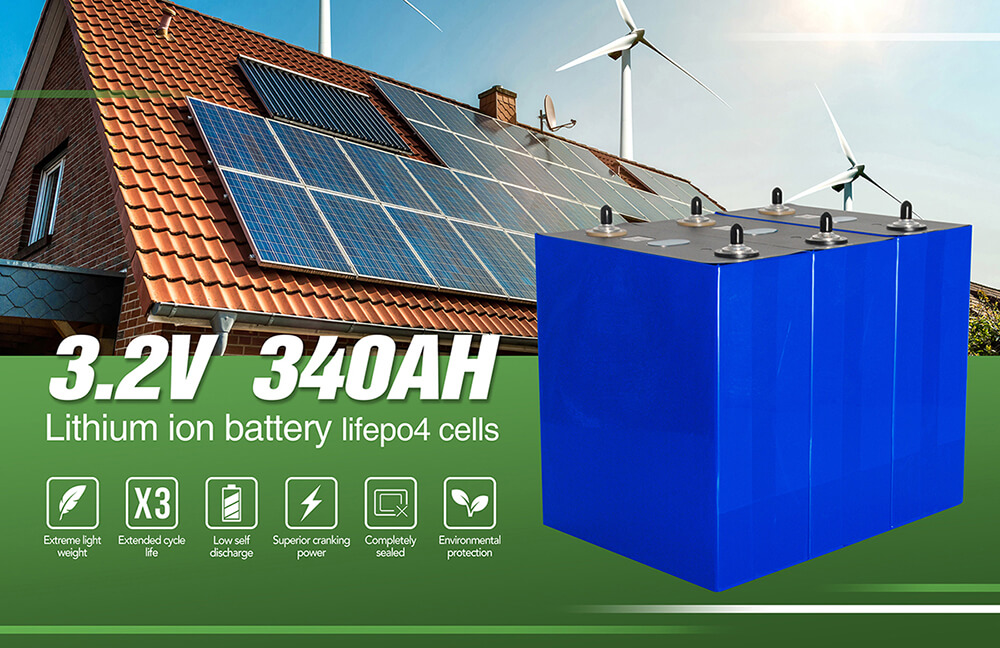
LiFePO4 Battery Cells
1. Acquisition and preparation of raw materials: This subheading encompasses the initial stages of the manufacturing process for LiFePO4 batteries, which involves obtaining the necessary raw materials and preparing them for use.
- Raw Material Sourcing: The first step in this process is to source the raw materials required for manufacturing LiFePO4 batteries. This may involve obtaining lithium, iron, phosphate, and other materials from various sources, such as mines, refineries, or suppliers. The materials must meet the required specifications and quality standards for battery production.
- Material Characterization: Once the raw materials are obtained, they need to be characterized to determine their properties and quality. This may involve conducting tests and analysis to ensure that the materials meet the required specifications, such as chemical composition, particle size, and purity. Material characterization is important to ensure that the raw materials are suitable for use in battery manufacturing and to maintain consistency and reliability in the final product.
- Raw Material Processing: After characterization, the raw materials may need to undergo processing to refine them and prepare them for use in battery production. For example, lithium may need to be processed to obtain lithium carbonate or lithium hydroxide, which are commonly used as raw materials for LiFePO4 batteries. Similarly, iron and phosphate may require processing to remove impurities and achieve the desired chemical composition.
- Material Formulation: Once the raw materials are processed, they may be formulated into a specific composition to create the battery's active materials. This may involve blending the processed materials in precise proportions to achieve the desired chemical composition and performance characteristics of the LiFePO4 battery. Binders and conductive additives may also be added to the formulation to improve the electrode's properties and performance.
- Material Handling and Storage: Proper handling and storage of the raw materials are essential to maintain their quality and prevent contamination. This may involve following established procedures for material handling, such as using protective equipment, storing materials in appropriate containers, and implementing proper labeling and identification. Strict quality control measures may also be in place to ensure that the raw materials are stored in controlled environments to prevent degradation or spoilage.
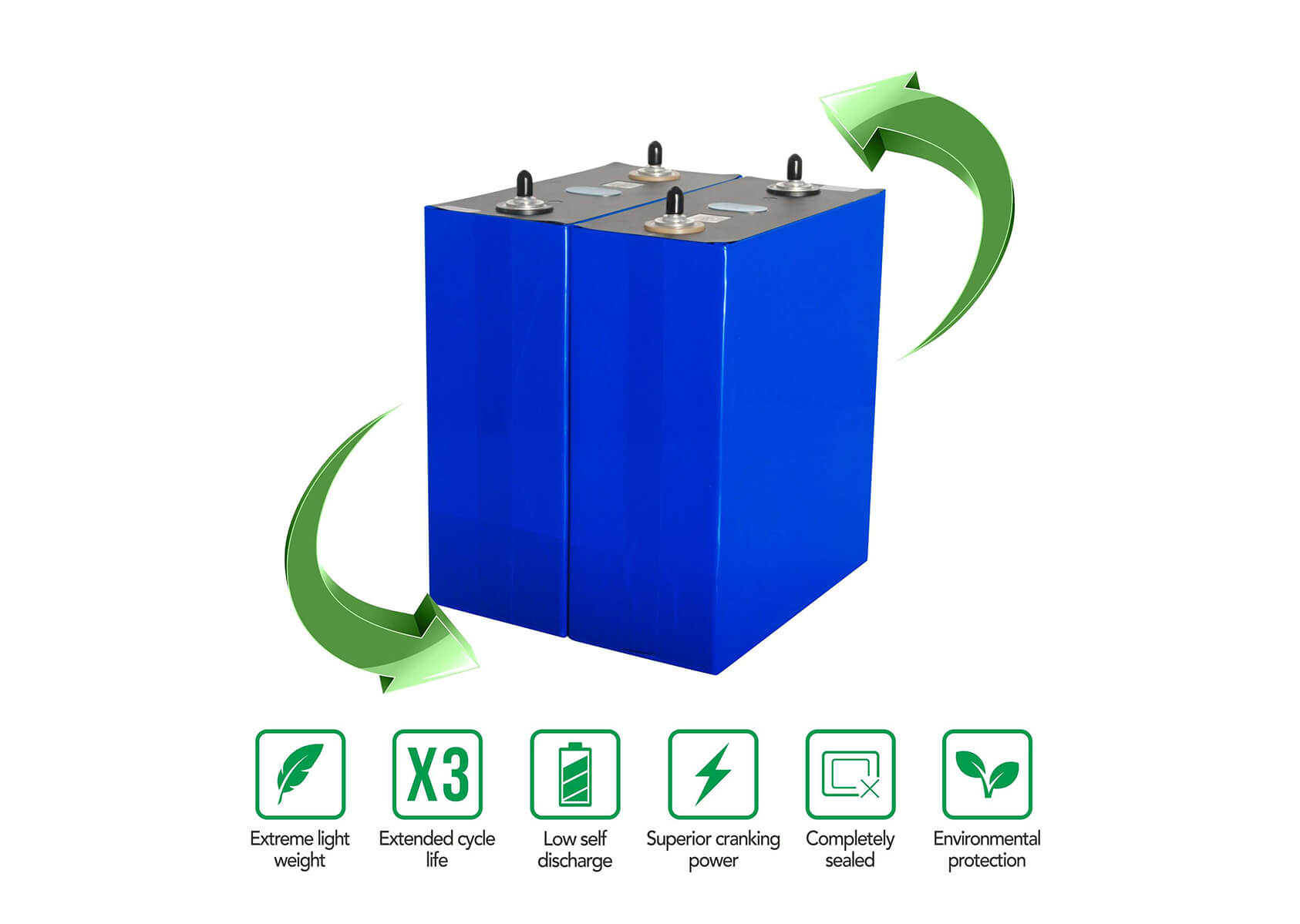
2. Electrode Fabrication and Assembly: This subheading encompasses the crucial steps involved in creating the electrodes, which are one of the key components of a LiFePO4 battery. The electrode fabrication and assembly process typically includes the following steps:
- Active Material Mixing: The first step in electrode fabrication is to mix the active materials, which are typically LiFePO4 for the cathode and a carbon-based material for the anode, with binders and conductive additives. Binders are used to hold the active materials together and improve their adhesion to the current collector, while conductive additives enhance the electrode's electrical conductivity.
- Coating the Active Materials: Once the active material mixture is prepared, it is coated onto a current collector, which is typically made of aluminum for the cathode and copper for the anode. The coating process may involve techniques such as doctor blade coating, roll-to-roll coating, or screen printing, which ensures a uniform and controlled thickness of the active material layer on the current collector.
- Drying and Calendaring: After the active material is coated onto the current collector, it is typically dried to remove solvents and binders. Calendaring, which involves pressing the electrode to a specific thickness, may also be performed to improve the electrode's mechanical integrity and optimize its performance.
- Electrode Stacking: Once the cathode and anode electrodes are fabricated, they are stacked together with a separator in between to prevent short-circuiting. The separator is typically made of a porous material that allows the flow of lithium ions while preventing direct contact between the electrodes. The electrodes and separator are then pressed together to form a compact electrode stack.
- Welding or Tabbing: The electrode stack may have tabs or foils attached to the current collectors to serve as electrical connections. This can be done through processes such as laser welding or tabbing, where metal foils or tabs are attached to the current collectors to facilitate the flow of electrical current within the battery cell.
- Assembly into Battery Cell: The final step in electrode fabrication and assembly is to assemble the complete battery cell. The electrode stack, along with the separator, is assembled into a cylindrical or prismatic cell container, and then it is filled with the electrolyte, which is the conducting medium for lithium ions. The cell is then sealed to prevent leakage and to ensure the safety and performance of the LiFePO4 battery.
- Electrolyte Preparation and Cell Formation: This subheading focuses on the crucial steps involved in preparing the electrolyte and forming the battery cells in the manufacturing process of LiFePO4 batteries. The electrolyte preparation and cell formation process typically includes the following steps:
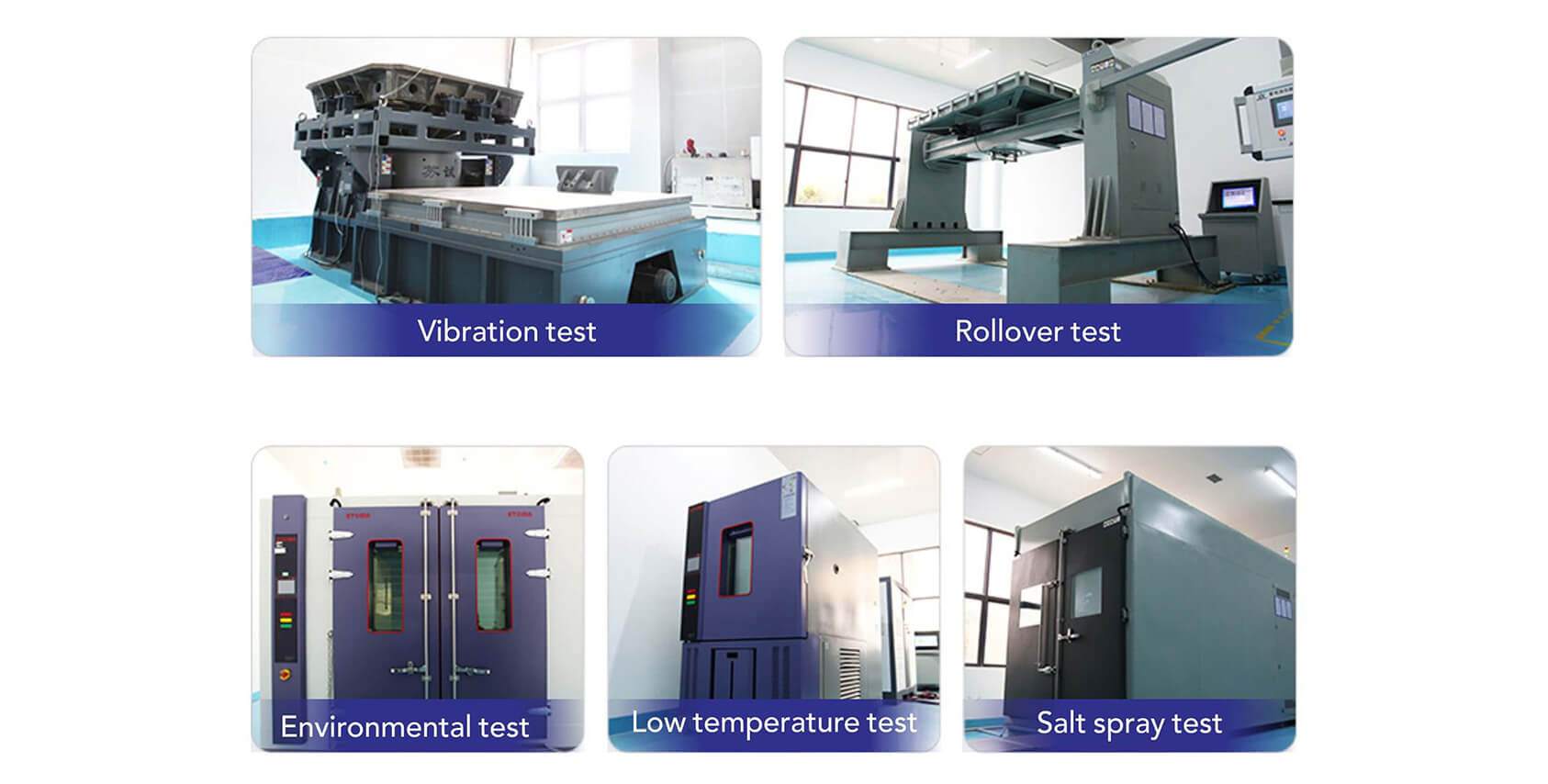
3. Electrolyte Mixing: The first step in electrolyte preparation is to mix electrolyte salts with solvents to create the electrolyte solution. The electrolyte salts are typically lithium salts, such as lithium hexafluorophosphate (LiPF6) or lithium bis(trifluoromethanesulfonyl)imide (LiTFSI), and the solvents are typically a mixture of organic solvents, such as ethylene carbonate (EC), diethyl carbonate (DEC), dimethyl carbonate (DMC), and/or other co-solvents. The electrolyte solution is carefully formulated to achieve the desired electrochemical properties and performance of the LiFePO4 battery.
- Filtering and Degassing: After the electrolyte solution is mixed, it may undergo filtering and degassing processes to remove impurities and trapped gases. Filtering helps to ensure that the electrolyte is free from particles or contaminants that could affect the performance or safety of the battery. Degassing is performed to remove any dissolved gases, such as oxygen and moisture, which could potentially react with the battery components and cause degradation or safety issues.
- Cell Formation: The cell formation process involves stacking and compressing the electrodes along with separators to create the battery cells. The prepared cathode and anode electrodes, along with a separator that prevents short-circuiting, are carefully stacked in a specific sequence to form a complete cell assembly. The cell assembly is then compressed to ensure proper contact between the electrodes and the separator.
- Electrolyte Filling: Once the cell assembly is formed, it is filled with the prepared electrolyte solution. This can be done through various methods such as vacuum filling, injection filling, or soaking. Care must be taken to ensure that the electrolyte is evenly distributed throughout the cell and that the proper electrolyte volume is added to achieve the desired cell performance.
- Sealing and Formation: After the electrolyte is filled, the battery cells are sealed to prevent leakage and to ensure the safety and performance of the LiFePO4 batteries. The sealed cells may then undergo a formation process, which involves applying a specific voltage and current profile to the cells to condition them and stabilize their performance. The formation process is critical in optimizing the capacity, cycle life, and safety of the LiFePO4 batteries.
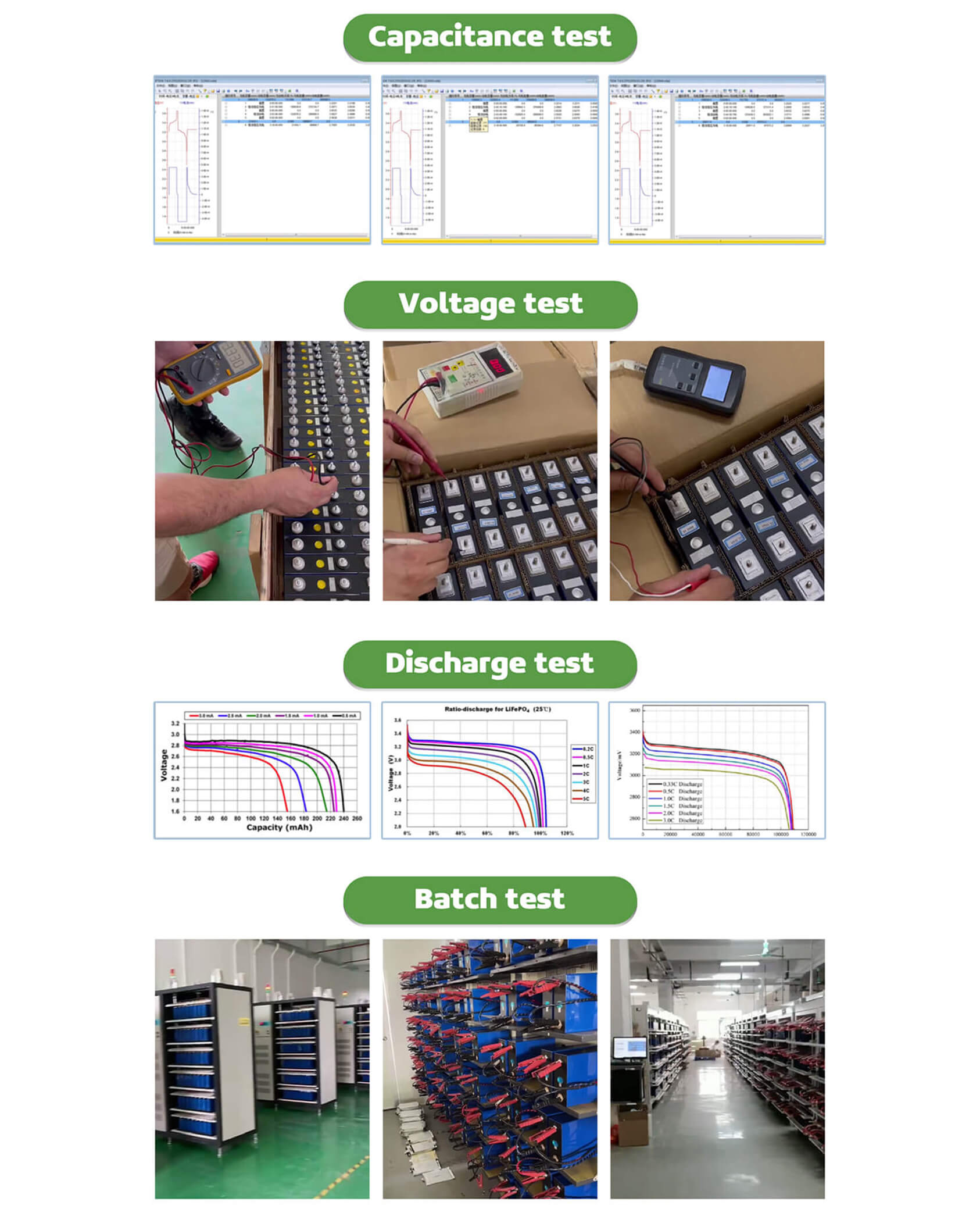
4. Battery Testing, Packaging, and Quality Control: This subheading covers the final stages of the LiFePO4 battery manufacturing process, which includes testing, packaging, and ensuring quality control. The steps involved in this subheading may include:
- Performance and Safety Testing: Once the LiFePO4 batteries are assembled, they undergo comprehensive performance and safety testing. This may involve measuring the battery's capacity, voltage, internal resistance, and temperature characteristics to ensure that they meet the required specifications and performance standards. Additionally, various safety tests may be conducted, such as overcharge, over-discharge, and short-circuit tests, to verify the battery's safety features and compliance with safety regulations.
- Packaging: After the LiFePO4 batteries have passed the performance and safety testing, they are packaged into their final form. This may involve placing the batteries into protective cases, shrink-wrapping, or sealing them in plastic or metal containers, depending on the intended application and transportation requirements. Proper packaging is essential to protect the batteries from physical damage and environmental factors during storage, transportation, and handling.
- Quality Control: LiFePO4 batteries may undergo rigorous quality control inspections to ensure that they meet the established quality standards. This may involve visual inspection, functional testing, and other quality control measures to identify and rectify any defects or inconsistencies in the batteries' appearance, performance, or safety features. Quality control processes help to ensure that only batteries that meet the specified quality criteria are released for distribution and use.
- Labeling and Marking: As part of the battery manufacturing process, labeling and marking are important for identifying and providing information about the batteries. This may include labeling the batteries with their specifications, performance characteristics, safety warnings, and compliance markings according to relevant regulations and standards. Proper labeling and marking help in identifying the type and characteristics of the batteries, ensuring safe handling, and complying with regulatory requirements.